ダイレスNCフォーミング機は、専用金型を使わずに金属の薄板を3次元形状に成形できる画期的な装置です。産学官のパートナーシップ制度を利用し、新しい成形技術として研究が始められた逆張り出し成形法をいち早く取り入れ、試作や小ロッド生産向け工法の一つとして実現しました。X・Y軸の水平動作とZ軸の垂直動作、材料を固定するワークホルダの昇降機構で構成されており、ワークホルダに固定された材料が受け治具に押し当てられつつ、それら一体が水平移動し、Z軸の先端に取り付けられた成形工具が少しづつ垂直方向へ材料を伸ばし3次元の逐次成形を行います。
ダイレスNCフォーミング機の成形法では、工具と接触した部位の材料を変形させ、基本的には材料の流入・流出を抑制します。これによりプレス加工では実現の難しかった複雑な形状なども成形できます。また、あらかじめ計画していれば、受け治具やワークホルダなどを修正することなく、板厚や種類などが異なる材料の成形はもちろんのこと、プログラム変更だけで異形状の成形をすることも可能です。 成形工具によって伸ばされた部位の材料は板厚減少を起こしますが、未成形部は変形が無いことから板厚の減少もありません。この特性を利用すれば、すでに成形されたパネルや管鋼材などに対して、追加で成形することも可能です。 プレス加工と比べ省エネルギー、小スペース、低振動、低騒音で成形できます。一枚あたりの成形時間は必要となりますが、簡単な受け治具とワークホルダがあれば成形を開始することができるため、初品出しまでに費やす時間を大幅に短縮することができます。また、金型不要の為、低コストにて製品を取得することが可能です。これらの特徴は、ダイレスNCフォーミング機による逆張り出し逐次成形法および張り出し逐次成形法ならではの最大のメリットです。
ダイレスNCフォーミング機の成形法では、工具と接触した部位の材料を変形させ、基本的には材料の流入・流出を抑制します。これによりプレス加工では実現の難しかった複雑な形状なども成形できます。また、あらかじめ計画していれば、受け治具やワークホルダなどを修正することなく、板厚や種類などが異なる材料の成形はもちろんのこと、プログラム変更だけで異形状の成形をすることも可能です。 成形工具によって伸ばされた部位の材料は板厚減少を起こしますが、未成形部は変形が無いことから板厚の減少もありません。この特性を利用すれば、すでに成形されたパネルや管鋼材などに対して、追加で成形することも可能です。 プレス加工と比べ省エネルギー、小スペース、低振動、低騒音で成形できます。一枚あたりの成形時間は必要となりますが、簡単な受け治具とワークホルダがあれば成形を開始することができるため、初品出しまでに費やす時間を大幅に短縮することができます。また、金型不要の為、低コストにて製品を取得することが可能です。これらの特徴は、ダイレスNCフォーミング機による逆張り出し逐次成形法および張り出し逐次成形法ならではの最大のメリットです。
ダイレスNCフォーミング装置構図

成形中の様子
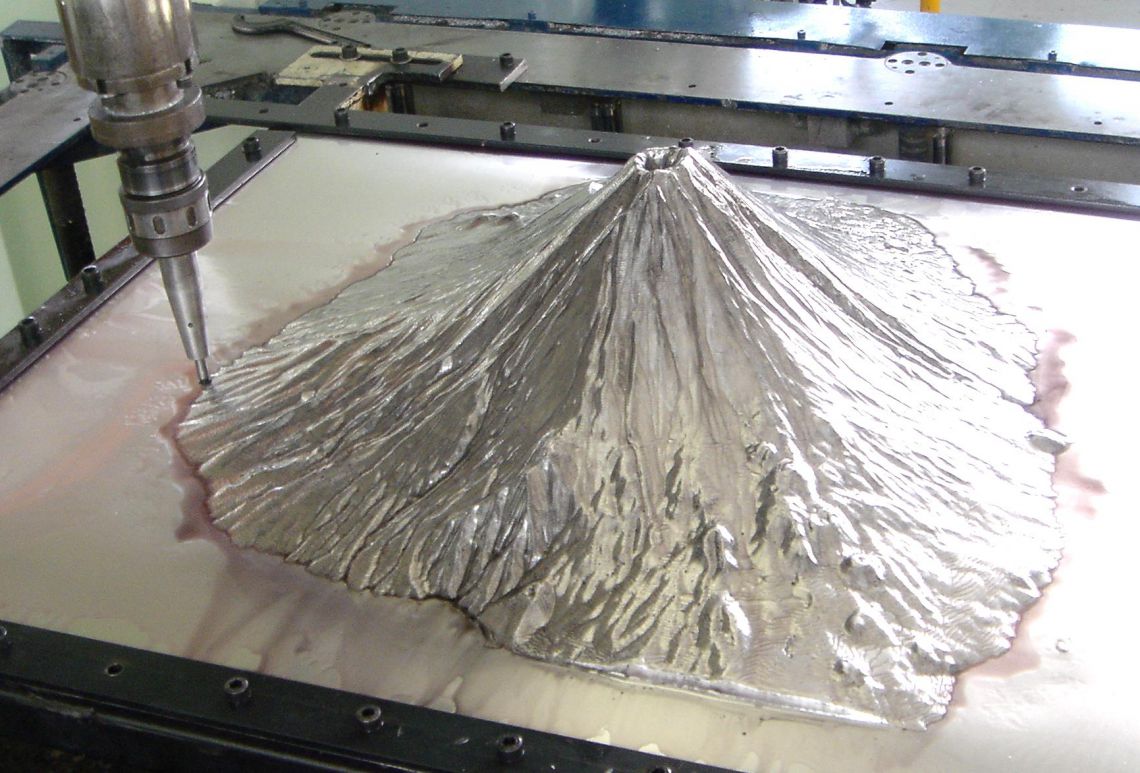
POINT
01
金属薄板の3次元成形が金型不要で可能
02
プレス加工と比べ、低出力・小スペース・低騒音・低振動
03
様々な形状に対応する高い自由度
04
試作品など初品出しまでの工期短縮
05
金型レス・工期短縮による試作開発費の削減
実例紹介
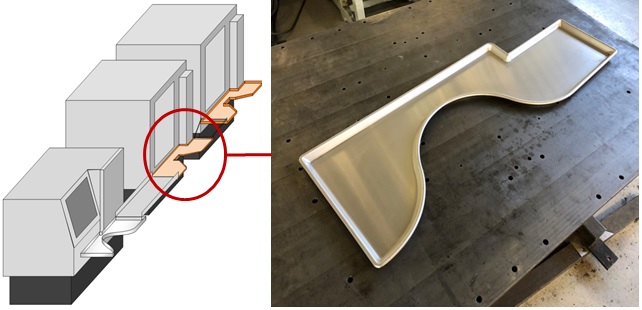
ある工場内で、加工品を次工程の加工機に移動させる際に切削油等が垂れるという問題があり、その対策として加工品の移動ルートには板金、溶接加工で製作したオイルパンを設置していました。この垂れた切削油には切粉等が含まれており、それらの除去に磁石を使用していたので、オイルパンには非磁性体のステンレスが使われていました。また、人が機械に接近しやすいように部分的に窪みがあるやや複雑な形状でした。製作方法を従来までの板金、溶接加工からダイレス成形に置き換えることで、形状の自由度が上がり、設置時の見た目や機能性、オイルパンの製作精度の向上に繋がりました。更に、金型(パンチ)を必要としないため低費用で形状が異なる複数のオイルパンを製作することができるようになりました。
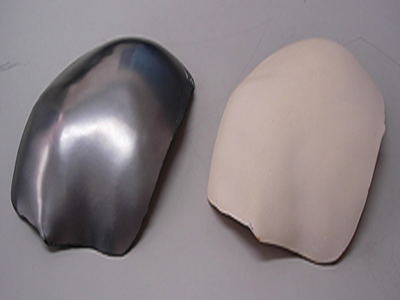
左は、医療用インプラント(頭蓋骨)を模したチタン素材製の試作品です。製品の特性上、形状は一品一様の完全オーダーメイドとなり、製作工期についても極めて短時間での対応が要求されるものになります。既存のプレス加工やハンドメイドではコストや工期において難しいとされていましたが、金型が不要であるダイレスNCフォーミングであればこのような難題にも柔軟な発想をもって対応致します。
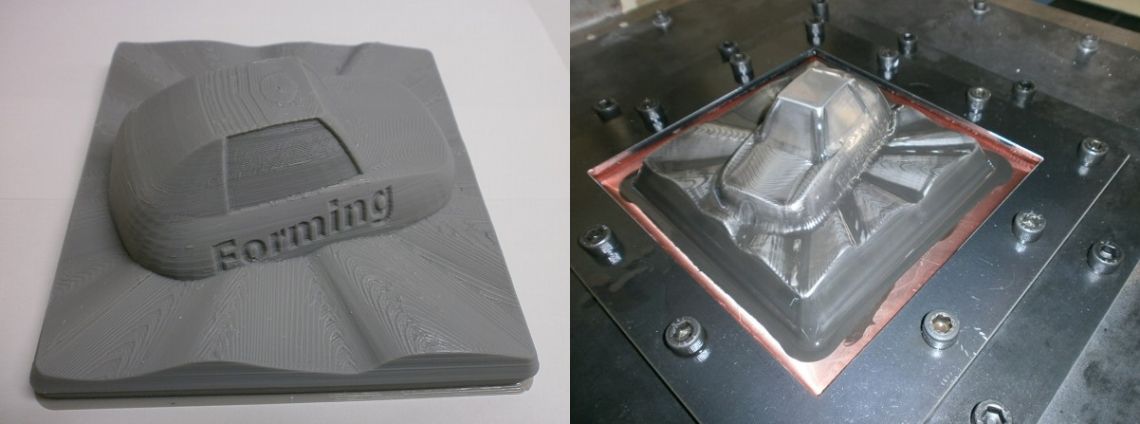
左は、3DプリンターでダイレスNCフォーミング用の冶具を試作・トライした成形品です。形状は自動車玩具を模しております。
冶具取付用の位置決め穴や、冶具固定面の平坦度が必要となりますが、個人でも冶具製作を行うことが出来るため、世界に一つだけのデザインを形にすることが出来ます。
これは、豊橋技術科学大学のインターンシップ生との成果例です。
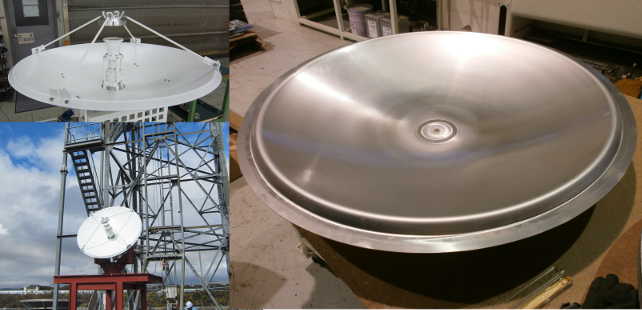
ダイレスNCフォーミング機のインクリメンタル成形で実現した製品事例を紹介します。本製品は生産台数が少ない特殊な仕様のパラボラアンテナです。このような製品を従来工法の金型を使ったプレス成形で開発・生産するとなると金型製作・メンテなど大きな負担となっておりましたが、本工法に置き換えることで費用を削減することが出来ました。
成形治具に関しては、土台となる板の中央に支柱を固定しただけの受け治具と、材料を固定するブランクホルダの2点で構成されています。受け治具に材料を上から押し付け、突っ張った材料に成形工具を押し当てて空中で成形しています。
成形治具に関しては、土台となる板の中央に支柱を固定しただけの受け治具と、材料を固定するブランクホルダの2点で構成されています。受け治具に材料を上から押し付け、突っ張った材料に成形工具を押し当てて空中で成形しています。